FAQs - Personal Protective Equipment
It's critical to keep your employees safe at work and adhere to relevant regulations. Here are a few commonly asked questions relating to PPE.
What regulations apply to PPE?
Regulation 2016/425 of the 9th of March 2016 on personal protective equipment, is the design manufacture and marketing a personal protective equipment. It defines legal obligations to ensure that PPE on the EU international market provides the highest level of protection against risks.
What are the four types of PPE?
- Respiratory protection – for example disposable cartridge airline half a full face.
- Eye protection – for example spectacles/goggles, shields and visors.
- Hearing protection – for example, earmuffs and plugs.
- Hand protection – for example, gloves and barrier creams.
What function does PPE serve?
PPE is equipment that will protect the user against health and safety risks at work. It could include items such as safety helmets, gloves, eye protection, high visibility clothing, safety footwear and safety harnesses. It also includes respiratory protective equipment.
Is there a legal requirement to wear PPE?
Act 1974, section 7. This means they must follow safe systems of work on site rules required to protect the health and safety, including the compulsive use of personal protective equipment when deemed necessary through risk assessments, as required by the personal protective equipment at work regulations 1992.
A fundamental rule of thumb regarding PPE is that it should only be used as a last resort. All workplace risks should be identified and where sensible eliminated at source through technical or organisational means by providing protection on a collective basis (scaffolding instead of a harness).
If these measures are not sufficient, only then should PPE be used to protect against the hazards that are unavoidable.
PPE has it’s limitations because:
- PPE only protects the wearer
- It is less effective if not fitted properly
- The psychological effect of PPE may be such that the individual wearing the PPE feels more protected than he or she actually is.
Before buying PPE you should;
- Make an assessment of the hazards in the workplace to identify the correct type of PPE to be provided; and to ensure that PPE is appropriate to the risk.
- Care must be taken in selecting PPE as certain types give reasonably high levels of protection while others give relatively low levels of protection. The level of risk must be assessed so that the performance required of the PPE can be determined.
- PPE must be fitted correctly – employers should take into account the one type of PPE may not fit all
- In sourcing PPE, the employer must therefore, select appropriate PPE which is user-friendly and which fits the individual employee correctly
- Ensure any PPE you buy is the CE marked and complies with the requirements of the European Union regulations 2018, which require PPE to have the appropriate CE mark. The CE marking signifies that the PPE satisfies certain essential health and safety requirements
Who is responsible for paying for PPE?
The safety health and welfare at work act 2005, dictates that employers must supply PPE to employees were risk cannot be eliminated or adequately controlled. Employers cannot pass on to employees any financial costs associated with duties relating to safety, health and welfare at work. Unemployment may not ask for money to be paid to them by an employee for the provision of PPE whether returnable or otherwise.
Why is PPE so important?
Making the workplace safe includes providing instructions, procedures, training and supervision to encourage people to work safely and responsibly.
Even where engineering controls and safe systems of work have been applied, some hazards might remain. These include injuries to:
- the lungs, e.g. from breathing in contaminated air
- the head and feet, e.g. from falling materials
- the eyes, e.g. from flying particles or splashes of corrosive liquids
- the skin, e.g. from contact with corrosive materials
- the body, e.g. from extremes of heat or cold
PPE is needed in these cases to reduce the risk.
Who’s job is it to maintain my PPE?
It is the employers responsibility to maintain your PPE. PPE must be properly looked after and stored when not in use, e.g. in a dry, clean cupboard. If it is reusable it must be cleaned and kept in good condition.
Think about:
- using the right replacement parts which match the original, e.g. respirator filters
- keeping replacement PPE available
- who is responsible for maintenance and how it is to be done
- having a supply of appropriate disposable suits which are useful for dirty jobs where laundry costs are high, e.g. for visitors who need protective clothing
It is however the employees responsibility to make proper use of PPE and report its loss or destruction or any fault in it.
Do I need to wear my PPE for a quick job?
Absolutely yes! Never not wear your PPE for a job that only takes a few minutes.
You can find out more at the HSE website.
Improve Workplace Safety With Proper PPE with These 6 Tips
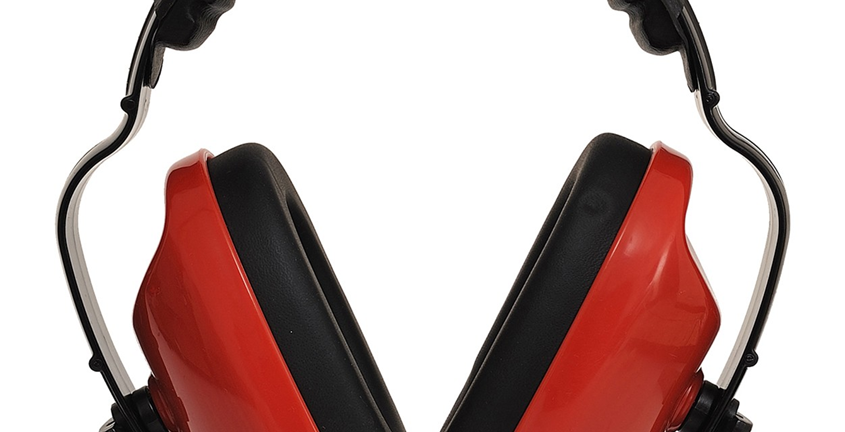
1.Understand the Role of Your Personal Protective Equipment (PPE).
Each type of PPE is engineered to protect workers against occupational hazards. Safety glasses protect a worker’s eyes from contact by objects and debris. Wraparound goggles provide side protection and some designs will reduce liquid and vapor penetration. Laboratory coats and secondary disposable PPE wear may offer protection against chemical spills, splashes and arc flash hazards. However, the correct fabric and materials must be selected, as not all apparel meets proper repellent and flame test standards.
Gloves should be selected carefully for the types of hazards present of the job. Cut-resistant gloves are needed around sharp machinery, while chemical-resistant gloves are needed for lab and some manufacturing work.
2. Know the Situations When PPE Should Be Used.
Following HSE guidelines is the recommended action for deciding what PPE should be used and when it is required. In any area where workers face airborne debris, safety glasses must be used. Hard hats are required for construction sites and any environments where workers face the hazard of falling objects. Protective apparel, gloves, boots and masks are required in many different operations including those that involve chemicals and flame / burn hazards.
3. Design a PPE Program.
Employers are required to provide workers with the tools and safety equipment needed to perform their jobs. Training requirements include knowing when the PPE is needed and what type is required.
Employees must understand how to use or wear safety equipment. If it is not used correctly, it does not provide necessary protection.
This training program should also include how to inspect equipment and when new PPE should be requested. Checklists should be made available to supervisors and one or more individuals assigned to maintain training records and assurance programs.
4. Understand the Necessary Steps in Selecting Appropriate PPE for Your Work Environment.
You want your PPE to actually provide protection and it will not do this if it is substandard. When you select equipment, you must pay attention to the manufacturer’s ratings and test results. Testing that is conducted in situations that simulate how the garment or other PPE is to be worn in actual workplace scenarios produce the most accurate performance ratings. Make sure that each piece of PPE meets current guidelines.
Check out the manufacturer of the product and what compliance ratings the equipment is designed to meet. Just because an item is fire resistant does not mean that it is appropriate in the workplace. Additionally, read the labels for contents. Fabrics designed to protect against a chemical spill are not always the same as those designed to protect against flame.
Many disposable garments claim to meet current standards but offer little protection to repel hazardous and non-hazardous chemicals as well as melt when exposed to flame. The items you choose for PPE must meet the hazards of your workplace.
5. Obtain Program Support and Promote Internally.
All employees in a facility must be involved in safety training for any areas where they work. Safety training is mandatory and managers and supervisors should be onboard when it comes to PPE requirements.
Holding training sessions and meetings can get the safety program started. All employees must be held accountable for the use of PPE once they have signed training documents.
6. Perform Regular Maintenance Inspections.
Like most equipment, PPE will wear out over time. Many items have expiration dates and must be removed from service after this date. A hard hat should be in use for no longer than five years and the date it is first placed ins service should be recorded inside the hat. Some PPE items are required to be replaced after an incident or if it becomes soiled to ensure protection for the wearer is not compromised.
While PPE protects you in the event of an accident, it does not prevent the accident itself. By establishing safety guidelines and training workers in the correct use of PPE, your facility will be safer and any accidents will be less likely to end in injury.